
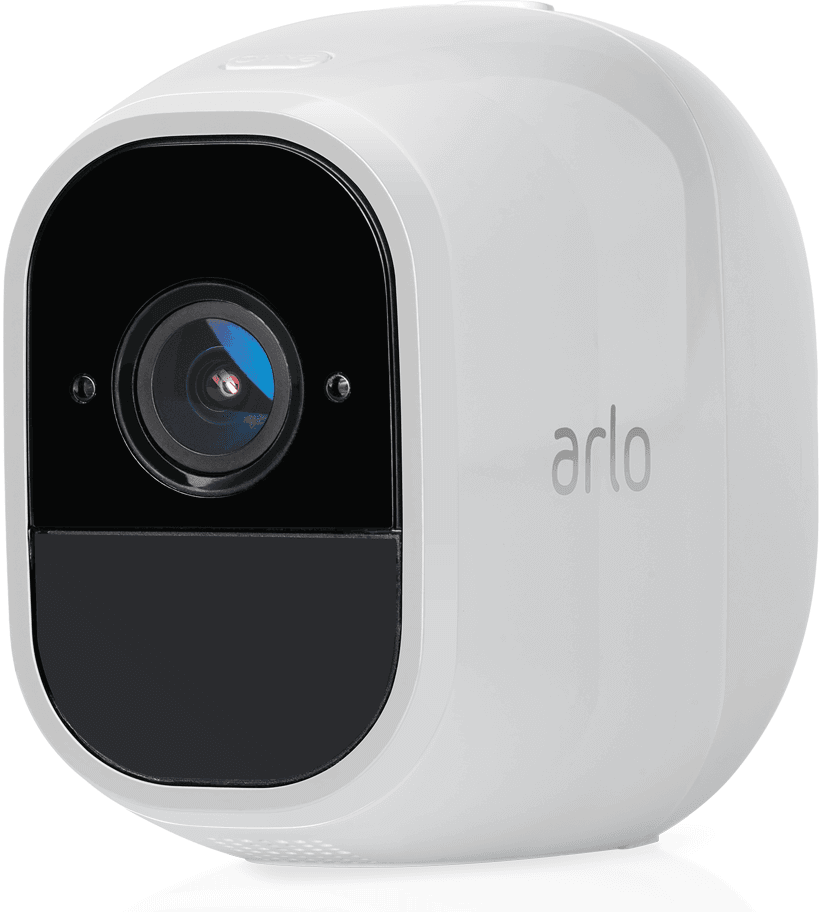
However, only a handful of attempts to adapt through-flow codes to simulate post-stall transients have been reported in open literature so far, with various level of accuracy, from 2D codes ( Escuret and Garnier, 1994) to 3D codes ( Gong, 1999 Longley, 2007). Through-flow codes are widely used to predict the design and off-design compressor performance. These codes offer a much smaller computational cost, but at the expense of the resolution inside of the blade passages, and require some method to estimate the blade row performance.
#Pro ii simulation two compressor code
Full-annulus URANS simulations have been carried out by ( Zhao et al., 2018) using the code AU3D, which successfully modelled a deep surge event and full-span rotating stall of a modern, high-speed, multi-stage, core compressor.Īn alternative to high-fidelity CFD can be offered by through-flow codes, in which the blade rows are not represented in the domain but their effect is introduced in the equations itself, often by means of source terms. Three-dimensional URANS simulations of post-stall transients require very large computational power and most models found in recent publications have attempted to reduce the size of the domain, for example by modelling a single passage ( Giersch et al., 2014), part of the annulus ( Crevel et al., 2014), or using a hybrid backward difference formula/harmonic balance method ( Sun et al., 2019). Research has therefore focused on numerical simulations of compressor stall, with both high-fidelity and low-order models.Įxample of rotating stall and deep surge trajectories on the compressor map, with phases of surge highlighted. Furthermore, tests cannot be used to predict the behaviour of a new geometry in the early stage of design. Experimental testing of compressor stall is very challenging: costs are prohibitive, flow measurements are limited and difficult, and results are often influenced by the specific rig set-up. For these reasons, the knowledge of the post-stall behaviour of compressors is of particular interest for engine manufacturers.
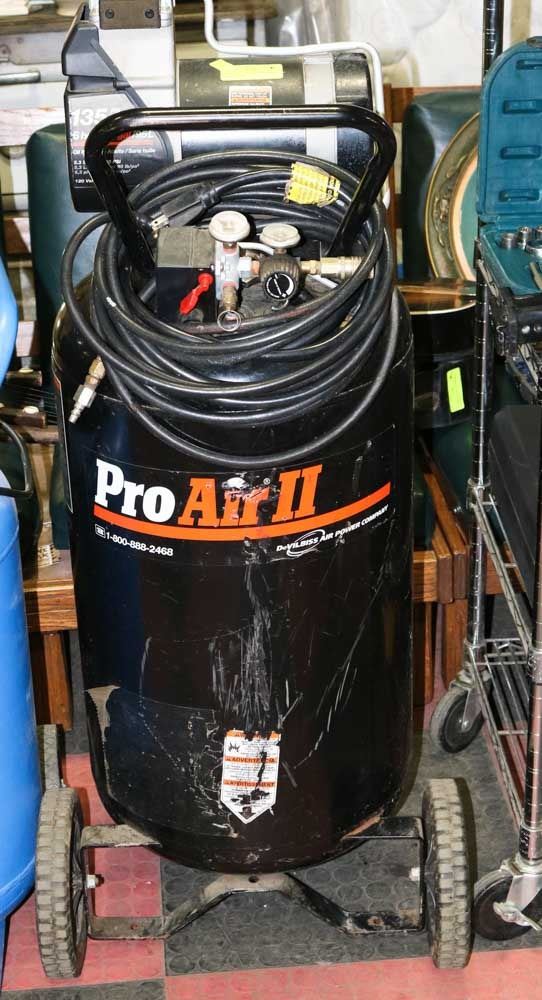
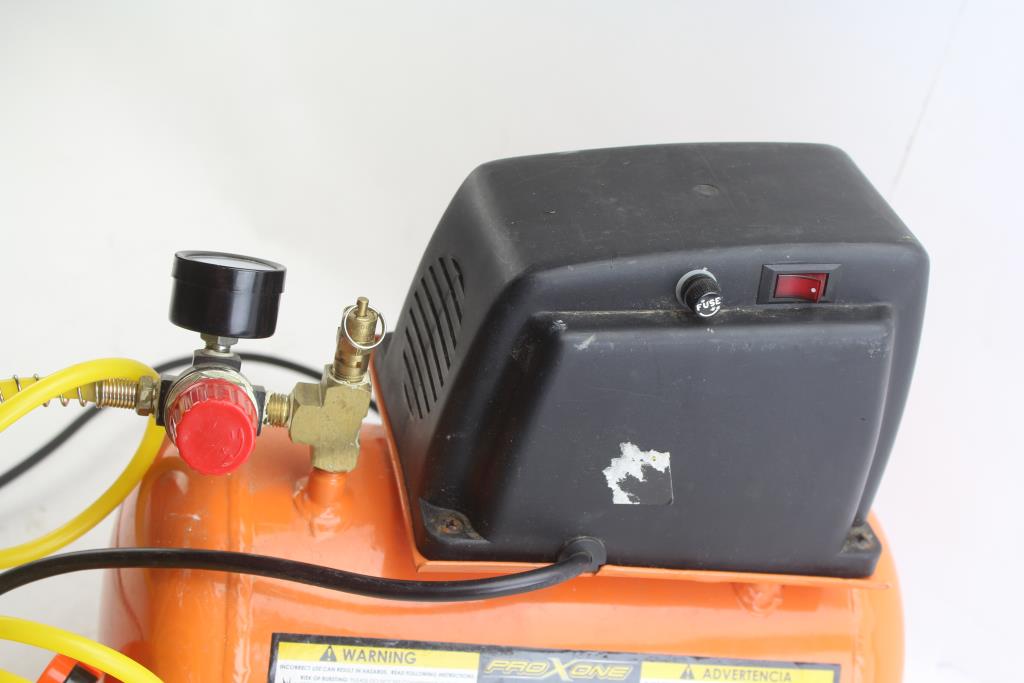
All types of compressor stall impose strong mechanical and thermal loads and can cause catastrophic damage to the engine, thus requiring the compressor design to sacrifice performance and weight to maintain a large surge margin. Deep surge itself is divided into 4 phases: reversal, blowdown, recovery and re-pressurization. Surge is distinguished between deep surge, when the massflow measured becomes temporarily negative, and classic surge when this does not occur. These two types of stall follow a well-known trajectory on the compressor map, as shown in Figure 1. Rotating stall is characterized by one or more cells of reversed flow rotating at a fraction of the rotor speed while surge is characterized by an axi-symmetric flow reversal. The post-stall behaviour of a compressor can be categorized into 2 types: rotating stall and surge. The operation of a modern jet engine is carefully limited to avoid the occurrence of compressor stall, an unstable disruption of the air flow inside of the compressor(s) which can cause temporary or permanent loss of propulsion. The low-order model is shown capable of predicting many transient flow features which were observed in the high-fidelity simulations, while reducing the computational cost by up to two orders of magnitude. Comparison of massflow, pressure and temperature time histories shows a close match between the low-order and the higher-fidelity methods.
#Pro ii simulation two compressor full
The results are compared against high-fidelity, full annulus, URANS simulations conducted at Imperial College. Two deep surge events are modelled at part speed and full speed respectively. The geometry investigated is an 8-stage rig representative of a modern aero-engine IP compressor. This paper describes the validation of an unsteady 3D through-flow code developed at Cranfield University for the low-order modelling of surge in axial compressors. There is therefore an interest in developing a low-order model which can predict compressor performance during surge with sufficient accuracy at significantly reduced computational cost. While useful for the investigation of specific cases, costly experimental tests and high-fidelity CFD simulations cannot be used routinely in the design process of compressor systems. Knowledge of unsteady performance and loading during surge is crucial for compressor design, however, the understanding and prediction capability for this phenomenon is still very limited. Surge in modern aero-engines can lead to violent disruption of the flow, damage to the blade structures and eventually engine shutdown.
